本文根據(jù)多年來對(duì)大型水泥回轉(zhuǎn)窯窯襯材料的使用情況以及各種材料的性能分析,研制適合大型水泥回轉(zhuǎn)過渡帶、分解帶的新型窯襯材料高活性相結(jié)合復(fù)合磚。
研制背景
在新型干法水泥回轉(zhuǎn)窯窯襯中,過渡帶是窯內(nèi)最易損毀的部位。由于窯內(nèi)熱工制度波動(dòng)頻繁,該處襯體的熱端面始終處于浮窯皮和無窯皮狀態(tài),一方面受到窯皮及水泥料的侵蝕、磨損,另一方面承受頻繁的熱沖擊,工作條件非常惡劣。
目前,新型干法水泥回轉(zhuǎn)窯過渡帶用材料通常為鎂鋁尖晶石磚、白云石磚、鎂鋁鉻磚及抗剝落高鋁磚等,其中日產(chǎn)2500噸以上的水泥回轉(zhuǎn)窯過渡帶大多采用鎂鋁尖晶石磚。鎂鋁尖晶石磚是以鎂砂和尖晶石為原料,經(jīng)高溫?zé)芍频茫淅砘笜?biāo)歸納見下表。
鎂鋁尖晶石磚在使用中表現(xiàn)出的損毀方式主要有以下幾種:
1、受水泥材料的化學(xué)侵蝕。
2、因高溫?zé)崤蛎浡瘦^大,導(dǎo)致襯體材料應(yīng)力集中,出現(xiàn)鎂鋁尖晶石磚的熱端剝落或棱角斷裂。
3、自身強(qiáng)度不高,磨損速率過快。
4、盡管含有一定的鎂鋁尖晶石相,材料熱震性得到改善,但由于是以MgO為主,熱震穩(wěn)定性仍存在不足;在受到頻繁溫度波動(dòng)條件下,材料強(qiáng)度下降,加劇了磨損速率。
另外,由于鎂鋁尖晶石磚的導(dǎo)熱系數(shù)較大,回轉(zhuǎn)窯筒體表面溫度較高,熱量散失大、易損壞窯體,同時(shí)也影響現(xiàn)場操作。
根據(jù)鎂鋁尖晶石磚的損毀機(jī)理及過渡帶工作條件,作為過渡帶材料應(yīng)具有如下優(yōu)點(diǎn):
1、抗水泥物料的化學(xué)侵蝕性好。
2、高溫?zé)崤蛎浡实?,保證砌體材料使用中應(yīng)力小,避免應(yīng)力損傷。
3、熱震穩(wěn)定性好。
4、強(qiáng)度高,耐磨性好。
5、導(dǎo)熱系數(shù)相對(duì)要低。
從過渡帶材料應(yīng)具有的優(yōu)點(diǎn)出發(fā),考慮到主要的損毀方式,研制一種新型的過渡帶材料—高活性相結(jié)合復(fù)合磚。
理論基礎(chǔ)
由過渡帶用鎂鋁尖晶石磚的損毀機(jī)理可知,其主要的損毀為應(yīng)力損傷、熱震剝落和化學(xué)侵蝕,其中應(yīng)力損傷和熱震剝落常導(dǎo)致材料使用中出現(xiàn)層狀脫落,使襯體材料厚度不能得到有效的利用,是較快的損毀方式;而這兩種損毀機(jī)制是由材料本身的固有性質(zhì)決定的。在以MgO為主體組份的材料中,MgO的熱膨脹系數(shù)為15-16×10-6(200~1000℃),在氧化物系耐火原料中可以說是非常高的,所以,鎂質(zhì)材料在頻繁的溫度波動(dòng)條件下,內(nèi)部產(chǎn)生較大的結(jié)構(gòu)應(yīng)力,制品強(qiáng)度下降或發(fā)生應(yīng)力損傷。
為從根本上減弱這種應(yīng)力,可選用線膨脹系數(shù)(α)較低的原料??紤]到新型干法水泥回轉(zhuǎn)窯過渡帶的使用條件,可以選用以Al2O3為主的原料,其中優(yōu)特礬土熟料在性價(jià)比方面比較適合。以MgO為主的鎂鋁尖晶石磚抗水泥料的侵蝕性較好,相比之下,以Al2O3為主的材料的抗侵蝕性則較弱,為此,在以優(yōu)特礬土為主的材料組份中引入第二種材料A。A為惰性材料,不與水泥熟料等發(fā)生化學(xué)反應(yīng),不會(huì)被侵蝕,如此,在一定程度上彌補(bǔ)了高鋁材料抗侵蝕性差的缺點(diǎn),使其抗侵蝕性得到一定的保障;同時(shí),A組份的線膨脹系數(shù)α較低,小于5.0×10-6(200~1000℃),這樣就可以保證復(fù)合材料在溫度波動(dòng)條件下的體積穩(wěn)定性,使材料具有較高的抗熱沖擊性能,同時(shí)也可以降低砌體應(yīng)力,保持砌體的完整性,從而解決了過渡帶用材料的熱震損毀和應(yīng)力損傷的問題。
由于A組份為惰性材料,與礬土熟料的反應(yīng)活性很低,所以,單獨(dú)將組份A與礬土熟料混合做成的制品是不會(huì)有強(qiáng)度的,也是無法使用的,為將二者有機(jī)地復(fù)合到一起,可采取兩種方式:
其一,加入粘土類低耐火相材料,依靠粘土的燒結(jié)將二者固定到一起;但這是依靠低熔點(diǎn)液相的作用,而低熔點(diǎn)玻璃相的存在對(duì)材料的高溫抗侵蝕性及抗磨損性都是非常 不利的。
其二,引入第三種材料HAP材料,HAP引入到礬土與惰性材料A的混合體中,經(jīng)中溫處理后轉(zhuǎn)變?yōu)楹苡袃r(jià)值的高活性組份,而此高活性相組份僅存在于1200℃以下,作為一種過渡的中間相;持續(xù)的升溫處理,則轉(zhuǎn)化為該復(fù)合材料的高強(qiáng)度結(jié)合相,從而將礬土熟料與惰性組份A牢固地結(jié)合到一起。在高強(qiáng)度結(jié)合相形成的過程中沒有液相的促進(jìn)燒結(jié)作用,完全是固固反應(yīng)機(jī)制,所以材料的強(qiáng)度較高,而且遠(yuǎn)高于鎂鋁尖晶石磚及鎂鉻磚;這對(duì)要求具有很好耐磨損性能的過渡帶來說是非常有利的。
由于礬土熟料中含有近2.0%的鐵,在燒成條件下,鐵將與Al2O3、SiO2等構(gòu)成液相存在,促進(jìn)燒結(jié),這一過程在以液相燒結(jié)機(jī)制為主的高溫處理過程中是可以的,但在高活性相結(jié)合復(fù)合磚的高溫?zé)芍袇s是不希望的。
引入HAP組份的高活性相結(jié)合復(fù)合磚的燒成過程中,應(yīng)控制磚內(nèi)氧分壓Po2/Po<10-17MPa,如此,則礬土熟料中的雜質(zhì)鐵等便起不到液相形成的促進(jìn)作用,也避免了形成的高強(qiáng)度結(jié)合相向液相中的溶解及二次再結(jié)晶,從而使材料保持較高的斷裂韌性、高溫強(qiáng)度及熱震穩(wěn)定性;同時(shí),組份A也能夠穩(wěn)定存在,制品能夠保持較好的抗水泥熟料的侵蝕性,所以,該復(fù)合磚完全可以取代鎂鋁尖晶石磚,其性能也優(yōu)于鎂鋁尖晶石磚,在過渡帶、冷卻帶上應(yīng)用是可行的,也是很有希望的。
鎂鉻磚和鎂鋁尖晶石磚同屬于富鎂材料,共同的不足就是熱膨脹率大、耐熱沖擊性不好。燒成帶鎂鉻磚主要就是由于這兩種因素的作用導(dǎo)致使用中出現(xiàn)的剝落損毀。過渡帶與燒成帶的工作條件有些近似,所以從理論上講,該活性相結(jié)合復(fù)合磚在燒成帶上的應(yīng)用也是可以的,而且部分性能還將優(yōu)于燒成鎂鉻磚。如果現(xiàn)場操作適當(dāng),壽命將高于鎂鉻磚。生產(chǎn)工藝
1.原料控制與顆粒級(jí)配
為了保證制品的質(zhì)量,原料進(jìn)廠后首先在本廠實(shí)驗(yàn)室進(jìn)行成份及相關(guān)性能測(cè)試。
原料的顆粒級(jí)配是影響制品性能的主要因素之一。考慮到制品的綜合性能,經(jīng)過實(shí)驗(yàn)篩選,高活性相結(jié)合復(fù)合磚的臨界顆粒尺寸以5~10mm為宜,粉料粒度以0.088~0.044mm為好。
高活性相結(jié)合復(fù)合磚采用機(jī)壓成型。混練出的泥料質(zhì)量對(duì)制品的性能影響很大,所以混練工序是很重要的工藝環(huán)節(jié)。具體操作為:
首先將顆粒料加入混練機(jī)中混練1~2分鐘,然后加入臨時(shí)結(jié)合劑混練1~2分鐘,再加入粉料混練4~6分鐘,泥料混練均勻后出料,此謂“初次混練”。為得到高質(zhì)量坯體,需將“初次混練”的泥料進(jìn)行“均化”處理后方能用于成型。所謂“均化”即是將經(jīng)過“初次混練”過的泥料進(jìn)行12~24小時(shí)的捆料后再進(jìn)行二次混練工藝。
2.成型
成型設(shè)備采用300~600t壓力機(jī)。成型沖壓先輕后重,短程多打。根據(jù)坯體的體積和與成型方向的尺寸來確定沖壓的次數(shù):一般厚度<65mm沖壓5~6次;厚度為65~68mm沖壓6~10次;厚度>85mm沖壓8~12次。要求坯體密實(shí)無磨面,無缺角少棱,坯體密度要求大于2.9~3.1g/cm3。
3.干燥與燒成
為了保證高活性相結(jié)合復(fù)合磚的成品質(zhì)量,對(duì)坯體必須進(jìn)行低溫烘干,烘干洞進(jìn)口溫度在30~55℃,高溫段80~110℃,出口溫度65~75℃。坯體在烘干洞里維持16~20小時(shí)。坯體殘余水份要小于1%,然后裝入窯中進(jìn)行燒成。由點(diǎn)燃到熄火的全過程用測(cè)溫錐和熱電偶控示。燒成溫度為139~1450℃,保溫8~12小時(shí)。
主要特點(diǎn)
高活性相結(jié)合復(fù)合磚與鎂鋁尖晶石磚的性能比較見下表。
從表中看出,除抗化學(xué)侵蝕性與鎂鋁尖晶石磚相當(dāng)外,其余指標(biāo)均優(yōu)于鎂鋁尖晶石磚,由此得到高活性相結(jié)合磚的主要特點(diǎn)為:
(1) 抗水泥料的化學(xué)侵蝕性較好。
(2) 高溫?zé)崤蛎浡实?,保證砌體材料使用中應(yīng)力小,避免應(yīng)力損壞。
(3) 熱震穩(wěn)定性好。
(4) 強(qiáng)度高,耐磨性好。
(5) 導(dǎo)熱系數(shù)低。
高活性相結(jié)合復(fù)合磚燒成過程中沒有液相的產(chǎn)生,完全依靠HAP組份中溫階段產(chǎn)生的固態(tài)高活性達(dá)到活性燒結(jié),繼而形成高強(qiáng)度結(jié)合相,避免了結(jié)合相向液相中溶解及二次再結(jié)晶,使材料保持了較高的斷裂韌性、強(qiáng)度及熱震穩(wěn)定性;惰性組份A的引入,使得制品保持了較好的抗化學(xué)侵蝕性;另外,該磚的最大優(yōu)點(diǎn)即是導(dǎo)熱系數(shù)比鎂鋁尖晶石磚小得多,降低了回轉(zhuǎn)窯筒體表面溫度,減少了熱量散失,節(jié)省了能源。
所以說,高活性相結(jié)合復(fù)合磚的性能優(yōu)于鎂鋁尖晶石磚和直接結(jié)合鎂鉻磚,在水泥回轉(zhuǎn)窯的過渡帶和冷卻帶完全可以替代鎂鋁尖晶石磚及鎂鉻磚;如果現(xiàn)場操作適當(dāng),可在燒成帶取代鎂鉻磚,而且還將具有比鎂鉻磚更好的抗剝落性能。
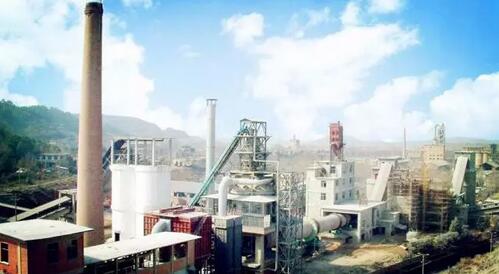
在新型干法水泥回轉(zhuǎn)窯窯襯中,過渡帶是窯內(nèi)最易損毀的部位。由于窯內(nèi)熱工制度波動(dòng)頻繁,該處襯體的熱端面始終處于浮窯皮和無窯皮狀態(tài),一方面受到窯皮及水泥料的侵蝕、磨損,另一方面承受頻繁的熱沖擊,工作條件非常惡劣。
目前,新型干法水泥回轉(zhuǎn)窯過渡帶用材料通常為鎂鋁尖晶石磚、白云石磚、鎂鋁鉻磚及抗剝落高鋁磚等,其中日產(chǎn)2500噸以上的水泥回轉(zhuǎn)窯過渡帶大多采用鎂鋁尖晶石磚。鎂鋁尖晶石磚是以鎂砂和尖晶石為原料,經(jīng)高溫?zé)芍频茫淅砘笜?biāo)歸納見下表。
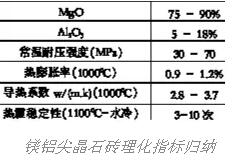
1、受水泥材料的化學(xué)侵蝕。
2、因高溫?zé)崤蛎浡瘦^大,導(dǎo)致襯體材料應(yīng)力集中,出現(xiàn)鎂鋁尖晶石磚的熱端剝落或棱角斷裂。
3、自身強(qiáng)度不高,磨損速率過快。
4、盡管含有一定的鎂鋁尖晶石相,材料熱震性得到改善,但由于是以MgO為主,熱震穩(wěn)定性仍存在不足;在受到頻繁溫度波動(dòng)條件下,材料強(qiáng)度下降,加劇了磨損速率。
另外,由于鎂鋁尖晶石磚的導(dǎo)熱系數(shù)較大,回轉(zhuǎn)窯筒體表面溫度較高,熱量散失大、易損壞窯體,同時(shí)也影響現(xiàn)場操作。
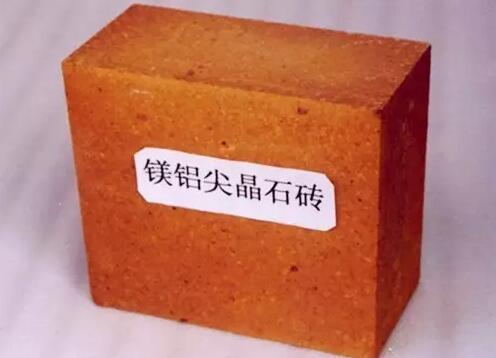
1、抗水泥物料的化學(xué)侵蝕性好。
2、高溫?zé)崤蛎浡实?,保證砌體材料使用中應(yīng)力小,避免應(yīng)力損傷。
3、熱震穩(wěn)定性好。
4、強(qiáng)度高,耐磨性好。
5、導(dǎo)熱系數(shù)相對(duì)要低。
從過渡帶材料應(yīng)具有的優(yōu)點(diǎn)出發(fā),考慮到主要的損毀方式,研制一種新型的過渡帶材料—高活性相結(jié)合復(fù)合磚。
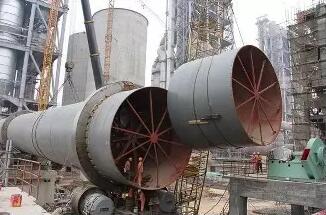
由過渡帶用鎂鋁尖晶石磚的損毀機(jī)理可知,其主要的損毀為應(yīng)力損傷、熱震剝落和化學(xué)侵蝕,其中應(yīng)力損傷和熱震剝落常導(dǎo)致材料使用中出現(xiàn)層狀脫落,使襯體材料厚度不能得到有效的利用,是較快的損毀方式;而這兩種損毀機(jī)制是由材料本身的固有性質(zhì)決定的。在以MgO為主體組份的材料中,MgO的熱膨脹系數(shù)為15-16×10-6(200~1000℃),在氧化物系耐火原料中可以說是非常高的,所以,鎂質(zhì)材料在頻繁的溫度波動(dòng)條件下,內(nèi)部產(chǎn)生較大的結(jié)構(gòu)應(yīng)力,制品強(qiáng)度下降或發(fā)生應(yīng)力損傷。
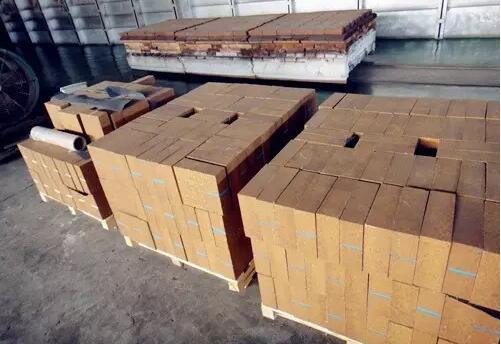
由于A組份為惰性材料,與礬土熟料的反應(yīng)活性很低,所以,單獨(dú)將組份A與礬土熟料混合做成的制品是不會(huì)有強(qiáng)度的,也是無法使用的,為將二者有機(jī)地復(fù)合到一起,可采取兩種方式:
其一,加入粘土類低耐火相材料,依靠粘土的燒結(jié)將二者固定到一起;但這是依靠低熔點(diǎn)液相的作用,而低熔點(diǎn)玻璃相的存在對(duì)材料的高溫抗侵蝕性及抗磨損性都是非常 不利的。
其二,引入第三種材料HAP材料,HAP引入到礬土與惰性材料A的混合體中,經(jīng)中溫處理后轉(zhuǎn)變?yōu)楹苡袃r(jià)值的高活性組份,而此高活性相組份僅存在于1200℃以下,作為一種過渡的中間相;持續(xù)的升溫處理,則轉(zhuǎn)化為該復(fù)合材料的高強(qiáng)度結(jié)合相,從而將礬土熟料與惰性組份A牢固地結(jié)合到一起。在高強(qiáng)度結(jié)合相形成的過程中沒有液相的促進(jìn)燒結(jié)作用,完全是固固反應(yīng)機(jī)制,所以材料的強(qiáng)度較高,而且遠(yuǎn)高于鎂鋁尖晶石磚及鎂鉻磚;這對(duì)要求具有很好耐磨損性能的過渡帶來說是非常有利的。
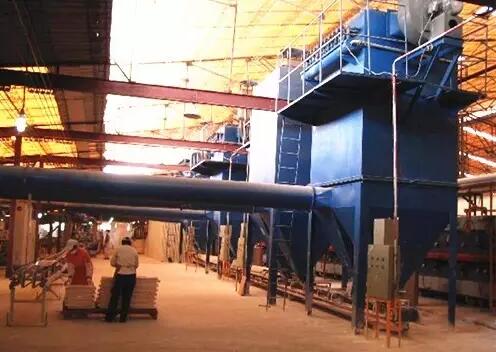
引入HAP組份的高活性相結(jié)合復(fù)合磚的燒成過程中,應(yīng)控制磚內(nèi)氧分壓Po2/Po<10-17MPa,如此,則礬土熟料中的雜質(zhì)鐵等便起不到液相形成的促進(jìn)作用,也避免了形成的高強(qiáng)度結(jié)合相向液相中的溶解及二次再結(jié)晶,從而使材料保持較高的斷裂韌性、高溫強(qiáng)度及熱震穩(wěn)定性;同時(shí),組份A也能夠穩(wěn)定存在,制品能夠保持較好的抗水泥熟料的侵蝕性,所以,該復(fù)合磚完全可以取代鎂鋁尖晶石磚,其性能也優(yōu)于鎂鋁尖晶石磚,在過渡帶、冷卻帶上應(yīng)用是可行的,也是很有希望的。
鎂鉻磚和鎂鋁尖晶石磚同屬于富鎂材料,共同的不足就是熱膨脹率大、耐熱沖擊性不好。燒成帶鎂鉻磚主要就是由于這兩種因素的作用導(dǎo)致使用中出現(xiàn)的剝落損毀。過渡帶與燒成帶的工作條件有些近似,所以從理論上講,該活性相結(jié)合復(fù)合磚在燒成帶上的應(yīng)用也是可以的,而且部分性能還將優(yōu)于燒成鎂鉻磚。如果現(xiàn)場操作適當(dāng),壽命將高于鎂鉻磚。生產(chǎn)工藝
1.原料控制與顆粒級(jí)配
為了保證制品的質(zhì)量,原料進(jìn)廠后首先在本廠實(shí)驗(yàn)室進(jìn)行成份及相關(guān)性能測(cè)試。
原料的顆粒級(jí)配是影響制品性能的主要因素之一。考慮到制品的綜合性能,經(jīng)過實(shí)驗(yàn)篩選,高活性相結(jié)合復(fù)合磚的臨界顆粒尺寸以5~10mm為宜,粉料粒度以0.088~0.044mm為好。
高活性相結(jié)合復(fù)合磚采用機(jī)壓成型。混練出的泥料質(zhì)量對(duì)制品的性能影響很大,所以混練工序是很重要的工藝環(huán)節(jié)。具體操作為:
首先將顆粒料加入混練機(jī)中混練1~2分鐘,然后加入臨時(shí)結(jié)合劑混練1~2分鐘,再加入粉料混練4~6分鐘,泥料混練均勻后出料,此謂“初次混練”。為得到高質(zhì)量坯體,需將“初次混練”的泥料進(jìn)行“均化”處理后方能用于成型。所謂“均化”即是將經(jīng)過“初次混練”過的泥料進(jìn)行12~24小時(shí)的捆料后再進(jìn)行二次混練工藝。
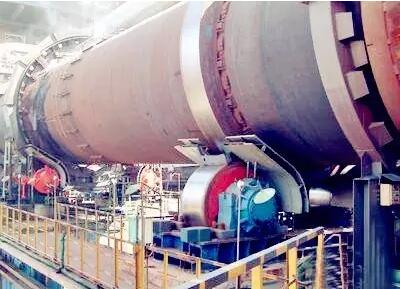
成型設(shè)備采用300~600t壓力機(jī)。成型沖壓先輕后重,短程多打。根據(jù)坯體的體積和與成型方向的尺寸來確定沖壓的次數(shù):一般厚度<65mm沖壓5~6次;厚度為65~68mm沖壓6~10次;厚度>85mm沖壓8~12次。要求坯體密實(shí)無磨面,無缺角少棱,坯體密度要求大于2.9~3.1g/cm3。
3.干燥與燒成
為了保證高活性相結(jié)合復(fù)合磚的成品質(zhì)量,對(duì)坯體必須進(jìn)行低溫烘干,烘干洞進(jìn)口溫度在30~55℃,高溫段80~110℃,出口溫度65~75℃。坯體在烘干洞里維持16~20小時(shí)。坯體殘余水份要小于1%,然后裝入窯中進(jìn)行燒成。由點(diǎn)燃到熄火的全過程用測(cè)溫錐和熱電偶控示。燒成溫度為139~1450℃,保溫8~12小時(shí)。
主要特點(diǎn)
高活性相結(jié)合復(fù)合磚與鎂鋁尖晶石磚的性能比較見下表。
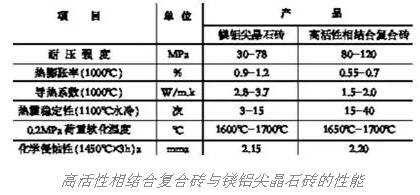
(1) 抗水泥料的化學(xué)侵蝕性較好。
(2) 高溫?zé)崤蛎浡实?,保證砌體材料使用中應(yīng)力小,避免應(yīng)力損壞。
(3) 熱震穩(wěn)定性好。
(4) 強(qiáng)度高,耐磨性好。
(5) 導(dǎo)熱系數(shù)低。
高活性相結(jié)合復(fù)合磚燒成過程中沒有液相的產(chǎn)生,完全依靠HAP組份中溫階段產(chǎn)生的固態(tài)高活性達(dá)到活性燒結(jié),繼而形成高強(qiáng)度結(jié)合相,避免了結(jié)合相向液相中溶解及二次再結(jié)晶,使材料保持了較高的斷裂韌性、強(qiáng)度及熱震穩(wěn)定性;惰性組份A的引入,使得制品保持了較好的抗化學(xué)侵蝕性;另外,該磚的最大優(yōu)點(diǎn)即是導(dǎo)熱系數(shù)比鎂鋁尖晶石磚小得多,降低了回轉(zhuǎn)窯筒體表面溫度,減少了熱量散失,節(jié)省了能源。
所以說,高活性相結(jié)合復(fù)合磚的性能優(yōu)于鎂鋁尖晶石磚和直接結(jié)合鎂鉻磚,在水泥回轉(zhuǎn)窯的過渡帶和冷卻帶完全可以替代鎂鋁尖晶石磚及鎂鉻磚;如果現(xiàn)場操作適當(dāng),可在燒成帶取代鎂鉻磚,而且還將具有比鎂鉻磚更好的抗剝落性能。