高爐發(fā)明的時期、地點目前尚不清楚,日本學者杉田清在著作中分析認為,在中世紀也就是大概14~15世紀,木炭在煉鐵中應用后,世界各地的煉鐵豎式爐逐漸演變、轉化為高爐,這便是高爐的原型。18世紀末19世紀初,焦炭、熱風爐及燒結礦、球團礦技術在高爐中的應用,標志著現(xiàn)代高爐的出現(xiàn)。之后經(jīng)過200多年的發(fā)展,煉鐵技術日臻完善,在這個過程中,作為輔助材料的耐火材料也取得了極大的進步,從最初使用云母頁巖和砂巖砌筑,到后來的黏土磚及現(xiàn)代的陶瓷杯材料及碳磚。本文簡要介紹了高爐爐缸陶瓷杯的出現(xiàn)過程,重點介紹了當代主流陶瓷杯制品的技術特點。
天然石英巖
這是中世紀時煉鐵用豎式爐、橫式爐所采用的一類耐火材料,主要采用天然石英巖或者同類的打結料作為耐火材料。這類耐火材料是中世紀煉鐵爐使用的主要耐火材料,一直到高爐原型即木炭型高爐的出現(xiàn),均以這類型材料作為主要的耐火材料,主要成分是高硅低鋁的天然原料,成分大概如表1所示。
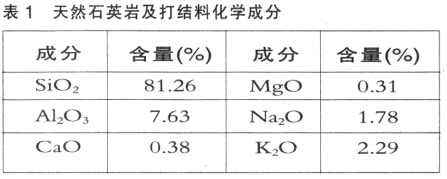
黏土磚
1709年AbrahamDarby實施以焦炭為還原劑的鐵礦石冶煉,帶來爐容積的擴大,對內(nèi)襯的可靠性要求提高,天然巖石及打結料內(nèi)襯無法滿足使用要求,逐漸消失。耐火磚成為爐襯的主體,材料中黏土質(zhì)(含有熟粘土、硅鋁類)成為主流,這種原料的使用特點一直持續(xù)到近代后期即第二次世界大戰(zhàn)結束。
之后被高品質(zhì)的剛玉質(zhì)陶瓷杯制品所取代,不過該類產(chǎn)品在高爐爐身等部位依然使用,在有些高爐中爐缸部位也使用一部分,不過其使用作用已經(jīng)和之前大不相同了,僅作為高爐點火調(diào)試用耐火材料,其主要作用是在調(diào)試過程中為之后高品質(zhì)的陶瓷杯制品及碳質(zhì)耐火材料提供保護,避免因調(diào)試產(chǎn)生劇烈的工況條件變化對耐材造成的破壞。
這類耐火材料現(xiàn)在具有的指標如表2(來源于冶標YB/T5050-93)。
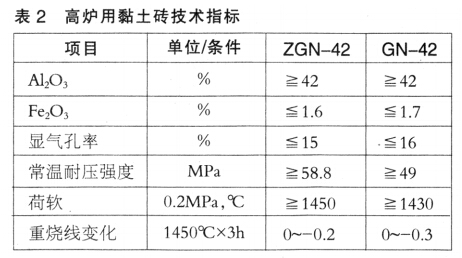
陶瓷杯的出現(xiàn)
及主流陶瓷杯制品的技術特點
煉鐵技術、設備的變化改變了對耐火材料的需求,推動了耐火材料的發(fā)展。在煉鐵方面,還有幾個非常重要具有里程碑式的發(fā)明或技術極大地提高了對耐火材料的要求,如:1857年,發(fā)明利用格子磚加熱空氣的專利,造出了熱風爐。1905年前后,燒結礦、球團礦工藝在高爐冶煉中得以應用。這兩個發(fā)明或者技術在高爐煉鐵中的應用,使得具有近代特征的高爐—熱風爐—焦爐—燒結機四位一體的“高爐系統(tǒng)”形成。爐缸熱負荷進一步提高,對耐火材料的要求進一步提高,之前的黏土磚無法承受高的熱負荷而失效,急需開發(fā)出具有更高性能的優(yōu)質(zhì)配套耐火材料。
恰逢此時基礎科學也取得了極大的發(fā)展,對耐火材料性能的改進提高提供了極大的幫助,世紀在物相平衡圖上的研究取得了極大的進展,首先是1919年C.N.Fenner研究了氧化硅相的關系,而這些物相的變化通過Chatelier的研究得以解釋和說明,這一研究使人們認識清楚了氧化硅的膨脹特性與物相的關系。1924年N.L.Bowen完成了Al2O3-SiO2相圖的繪制,該相圖的完成對這一體系耐火材料無疑具有非常重大的意義,使得人們找到了黏土磚隨氧化鋁含量增加耐火度隨之上升的真正原因。借助于這些研究成果,可得出提高氧化鋁來提高黏土磚耐火度以抵抗不斷提高的熱負荷的結論。終于Bauer等于1988年開發(fā)出陶瓷杯,一類以剛玉為主晶相的陶瓷杯制品,這類材料與炭磚共同砌筑組成爐缸爐襯,并在1988年的世界煉鐵會議上公布了其陶瓷杯配套產(chǎn)品的組成:陶瓷杯壁用磚有綠剛玉、灰剛玉、Sialon結合剛玉;杯墊用磚合成莫來石。各材料的指標見表3。
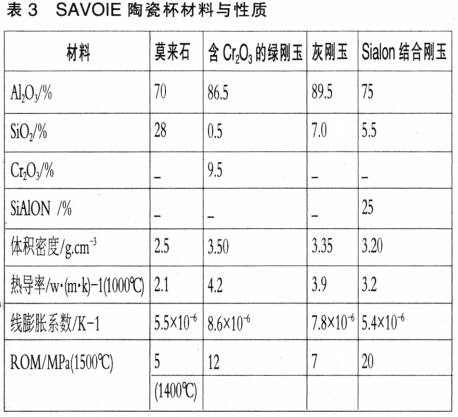
陶瓷杯杯壁最初設計使用的耐火磚為綠剛玉,使用這類型材料主要是從抗渣性方面出發(fā)考慮才選用的,Cr2O3與渣成分反應形成高黏度物相來覆蓋制品表面,阻止渣的進一步滲透。但是實際高爐條件下發(fā)現(xiàn)其表面形成的Al2O3-Cr2O3固溶體強度高、比較脆、膨脹較大,在溫度波動情況下會剝落,加劇損毀,實際使用效果受到影響,另外由于鎘污染,因此發(fā)展出莫來石結合的灰剛玉制品。這類制品具有適度的抗渣性能,同時表面不會形成脆性固溶體,有助于應力的釋放,綜合性能較好。杯壁的另一種配置是Sialon結合剛玉,這種非氧化物結合剛玉制品,抗渣性能更優(yōu),且這類產(chǎn)品強度高,熱膨脹系數(shù)小,抗熱震穩(wěn)定性要較灰剛玉制品更優(yōu)。
杯墊使用莫來石磚,爐底被熔融鐵水覆蓋,沒有熔渣及堿的侵蝕,莫來石磚荷軟高,耐鐵水熔蝕性能優(yōu),用于爐底能達到很好的使用效果。
鑒于法國陶瓷杯在高爐中使用業(yè)績較好,陶瓷杯技術上世紀90年代引入我國后,國內(nèi)有一些廠家積極開發(fā)配套耐材,在市場上使用較多且比較有代表性的有兩種,塑性相結合復合剛玉磚及微孔剛玉磚。
微孔剛玉磚技術指標如表4所示。微孔剛玉磚是國內(nèi)某廠2002年推出的一款產(chǎn)品,采用剛玉及莫來石為主要原料,以樹脂作為結合劑,于埋碳條件下進行燒成,磚中會殘留少量碳,并使磚具有微孔技術特點,這使得該磚的抗渣、堿性能會提高,實現(xiàn)較好的使用效果。
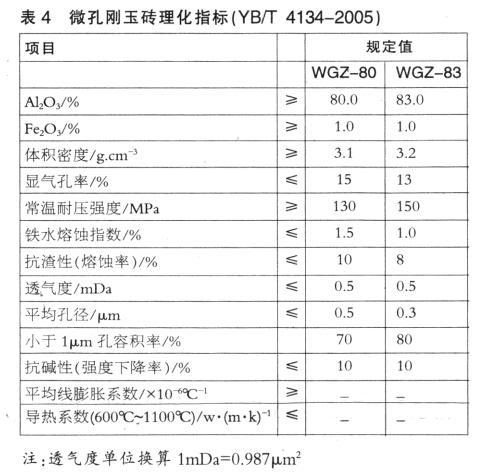
塑性相復合剛玉磚,是通達中原2001年推出的一款產(chǎn)品,是一種普遍應用的國產(chǎn)陶瓷杯用磚,以棕剛玉及碳化硅作為骨料,引入金屬硅,制備金屬塑性相剛玉復合材料,使制品兼具塑性相金屬及剛玉兩者的優(yōu)點。相應技術指標如表5所示。
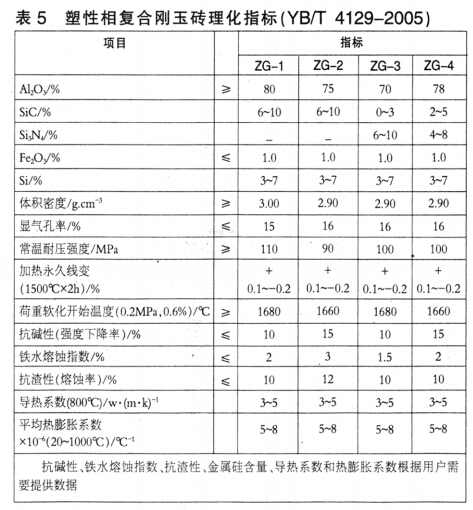
該制品具有以下技術特點:添加的金屬硅有促進燒結的作用,添加后制品的致密度提高。添加金屬硅作為塑性彌散相與耐火骨料及基質(zhì)復合,在外力作用下產(chǎn)生一定的塑性變形或沿晶界滑移分散集中的應力,使得斷裂能增大,引入金屬硅能達到增韌的效果。在磚中骨料與基質(zhì)的交界處恰好是應力集中區(qū),裂紋在這個區(qū)域容易擴展,而加入的金屬硅在1400℃以上時會變成液相填充在基質(zhì)與骨料之間的界面上。當裂紋尖端擴展抵達塑性相時,其應力將被吸收,阻止裂紋繼續(xù)發(fā)展,增強了材料的斷裂能,增強了材料抵抗熱應力的能力。這一技術方案解決了陶瓷質(zhì)耐火材料致密度提高與熱震穩(wěn)定性降低的矛盾。
燒結及使用過程中,塑性相金屬硅氧化形成的氧化硅與料中氧化鋁形成莫來石或玻璃相填充表面的氣孔,使得材料抗渣、堿滲透能力得到進一步提升。這也使得其在高爐中實現(xiàn)了良好的使用效果。
以上是兩種國產(chǎn)陶瓷杯杯壁用磚,對杯墊兩類磚均可使用,不過從實用角度來考慮,使用剛玉莫來石磚即可滿足使用,有些鋼鐵廠使用高鋁磚也實現(xiàn)了不錯的使用效果。
經(jīng)過40多年的發(fā)展,現(xiàn)在主流陶瓷杯制品如SAVOIE制品、微孔剛玉磚及塑性相結合復合剛玉磚,各有優(yōu)缺點,如果搭配合理并且能進行有效的維護,也能實現(xiàn)非常好的使用效果。
當然高爐長壽方面涉及的影響因素非常多而且非常復雜,耐火材料只是影響高爐壽命的一個因素,從提升耐火材料使用性能方面出發(fā)來延長高爐爐缸的使用壽命,依然是有空間的。
?